With spring break right around the corner, we and our classmates will be boarding planes, crossing state lines, and traversing the globe in order to have the best #SB2K16 we so desperately need. Some of us will be traveling to other continents, going home or seeing friends abroad, while others will be traveling to a tropical place to catch some rays. What we all have in common though, is that we will all be kicking off our spring breaks by going through security, getting side-eyed by the TSA, boarding a plane and taking our seats (probably a middle seat lets be honest). Once we take off we’ll probably take out our phones and put some music on and try to go to sleep since our flight boarded so early. What we won’t think about though is how our plane is going to stay safe throughout our flight and allow us to breathe as we soar thousands of feet above land and sea.
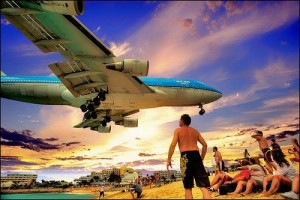
All planes are equipped with an environmental control system (ECS) that provides air supply, thermal control and cabin pressurization for the crew and passengers. The ECS is operated through a feedback system, therefore cabin pressurization and airflow is monitored and the air intake from the outside is adjusted accordingly. On aircrafts, air is supplied to the environmental control system by being “bled” from the compressor stage of a gas turbine engine. The temperature and pressure of the “bled” air varies depending on which stage of the compressor it is coming from, and the power setting that the engine is operating. To control cabin pressure, air conditioned air from the ECS is pumped into the cabin of a plane to create a safe and comfortable environment for passengers and crew flying at high altitudes. The air supplied to the fuselage is cooled, humidified, and mixed with recirculated air before it is distributed to the cabin. Pressurization is necessary at altitudes above 12,500 to 14,000 feet above sea level to protect passengers and crew from health problems caused by the low outside air pressure above those altitudes but is a requirement for cruising altitudes above 8,000 feet.
On the ground, the airplane is unpressurized and the outflow valve is wide open. During preflight, the pilot sets the cruise altitude on a cabin pressure controller. As soon as the weight is off the main wheels at takeoff, the outflow valve begins to close and the cabin starts to pressurize. The airplane may be climbing at thousands of feet per minute, but inside the cabin, the rate of “climb: is approximately what you might experience driving up a hill. It might take an average airliner about 20 minutes to reach a cruise altitude of approximately 35,000 feet, at which point the pressurization system maintains the cabin at the pressure you’d experience at 7,000 feet: about 11 pounds per square inch. Of course our ears may pop, however, the effect is mild because the rate of the climb is only about 350 feet per minute. When the airplane descends, the pilot sets the system controller to the altitude of the destination airport, and the process works in reverse.
The structural strength of the airplane determines how much differential pressure the cabin can tolerate—a typical figure is eight pounds per square inch—and the fuselages of new airplane designs are pressurized and depressurized many thousands of times during testing to ensure their integrity. The higher the maximum differential pressure, the closer to sea level the system can maintain the cabin. Federal Aviation Regulations say that without pressurization, pilots begin to need oxygen when they fly above 12,500 feet for more than 30 minutes, and passengers have to use it continuously above 15,000.
The structural strength of the airplane determines how much pressure the cabin can tolerate, a typical amount is about eight pounds per square inch, and the fuselages of new airplane designs are pressurized and depressurized many thousands of times during testing in order to ensure their integrity. Planes are designed so that occupants will not be exposed to altitudes over 25,000 feet for more than 2 minutes or at an altitude of 40,000 feet at any time. These regulations are in place in case of sudden decompression.
Pressurization is achieved by the design of an airtight fuselage engineered to be pressurized with a source of compressed air and controlled by an ecs. Air enters the system as bleed air which is extracted from the compressor stage of a gas turbine engine at a low stage and from an additional high stage. By the time the cold outside air has reached the bleed air valves, it is at a very high pressure and has been heated to about 200C. The control and selection of high or low bleed air sources is automatic and is governed by the requirements of various stages of flight. The part of the bleed air that is directed to the ecs is expanded and cooled to a suitable temperature by passing it though a heat exchanger and an air cycle machine called the packs system. At least 2 different engines provide the compressed bleed air for the plane’s ecs. Exhaust air is pumped into the atmosphere is an outflow valve, usually at the rear of the fuselage. This valve controls the cabin pressure and also acts as a safety relief valve. Is the automatic pressure controllers fail, the pilot can manually control the cabin pressure valve and the plane can still fly smoothly. The automatic controller normally maintains the proper cabin altitude by constantly adjusting the outflow valve position such that the cabin altitude pressure remains as low as possible without exceeding the limits of the fuselage.
Unplanned loss of cabin pressure at altitude is rare but has resulted in a number of fatal accidents. Failures range from sudden, catastrophic loss of airframe integrity, known as explosive decompression, to slow leaks or equipment malfunctions, that allow cabin pressure to drop undetected to levels that can lead to unconsciousness or severe performance degradation of the aircrew.
Any failure of cabin pressurization above 10,000 feet requires an emergency descent to approximately 8,000 feet or the closest to that while maintaining the Minimum Safe Altitude (MSA), and the deployment of an oxygen mask for each seat. The oxygen systems have sufficient oxygen for all on board and give the pilots adequate time to descend to below 8,000 ft. Without emergency oxygen, hypoxia may lead to loss of consciousness and a subsequent loss of control of the aircraft, since the time of useful consciousness varies according to altitude. As the pressure falls, the cabin air temperature may also plummet to the ambient outside temperature with a danger of hypothermia or frostbite. In jet fighter aircraft, the small size of the cockpit means that any decompression will be very rapid and would not allow the pilot time to put on an oxygen mask. Therefore, fighter jet pilots and aircrew are required to wear oxygen masks at all times.
So, the next time you’re on a flight and you’re thinking, “How the heck am I breathing right now?”, just refer to “The Mile High Club”, for everything you need to know about cabin pressure during air travel. Once you read it you’ll start to realize that it’s a very complicated process you may never fully understand, nor do you really want to because who wants to be paranoid about cabin pressure for a whole flight? As long as your pilot shows up sober, you should be fine!
This article analyzes the air system throughout a plane. I really enjoyed the intro into the actually blog post. It was both humorous and drew me into reading the rest of the post. The picture of how the air circulates the cabin from the engine was useful to look at as I was reading along next to it. I was unaware that this was how planes circulated air and kept us breathing and happy on long flights. I think that the planes could be modified to develop control parameters that would monitor exactly when air needed to be pumped through the cabin in order to not waste unnecessary energy (I am unsure if applications like this already exist or not). I definitely think that the public will use this device because we all fly on planes and it is something I rarely think about when experiencing it so it was an interesting read! It seems as though most of this is done manually which I think can definitely be improved. The height of the plane seems to be the disturbance variable since that was what affected the amount of pressurization was put into the plane. The manipulated variable is the amount of air that goes into the cabin to depressurize it control the air that we breathe. It seems as though there is already a system in place with a control that corrects for a failure of cabin pressure because the oxygen masks deploy after there is an emergency descent. I was not aware that jet pilots have to wear oxygen masks all the time but it makes sense after reading the article. I find it interesting that the pilot sets the system controller to the altitude of the destination airport. This must be the controlled variable (altitude) as well as it being the disturbance variable because if a plane starts to drop out of the sky, the altitude changes but suddenly. It says that as soon as the weight is off the main wheels at takeoff, the outflow valve begins to close and the cabin starts to pressurize, is this a control system? Or is this more of a mechanical system that they have in place to close the valve. I have a last question. If a bird gets stuck in the engine, obviously the engine will fail but will the air system also fail? Because it seems as though it would because the air that we are breathing on the plane is coming from the air that is arriving through the engine. I really enjoyed this article and I found it very informative. Good job!
I thought it was very interesting to learn about how the cabin of an airplane is pressurized, since as assumed in the blog post, it is something that never crossed my mind as I boarded my flight for #SB2K16. I knew that since air travel happens at extremely high altitudes, something happens to the cabin pressure, but I did not know how much goes into the actual pressurization control system. The information is presented in an entertaining way while still being informative and easy to understand, so good job there. I found it interesting that the “rate of climb” is relatively slow which is why we don’t experience too many harsh symptoms from the increase in pressure. The application of a control system to manipulate the cabin pressure is definitely useful in that it can literally save lives. It is definitely something that I, and the general public would use, since traveling is something that most people do and enjoy. It makes sense that this pressurization works using a feedback type of response, which would allow for the proper amount of pressurized air to be exactly right. From the article, it is implied that the control variable would be the cabin pressure, manipulated by the flow of pressurized air into the cabin through the valve system on the plane. The disturbance variable seems to be the pressure of the air outside the plane at a certain altitude. The chosen controlled, manipulated, and disturbance variables make sense, but I think it is a little unclear how the writers intend to change, or expand upon the current control system. I would suggest maybe elaborating on the new control system a little bit more. Since this system affects the health and safety of people, overshoot is probably not a good idea. Because of this, the proper controller gain needs to be chosen to avoid this issue. (It is probably preferred to have a slower time response rather than overshoot the amount of pressurized air pumped into the cabin.) I hope that I will never be on a flight where it will be necessary, but it is comforting to know that the pressurization system is very precise, and that the oxygen mask system in place provides enough oxygen for all passengers and crew members on board. Overall I think this was a very interesting and informative blog post! Nice work! (p.s. love the dad bod pic!!)
I enjoyed reading this blog article and was brought in by its humorous title. Title aside, this article spoke about a crucial feature of airplanes which is often ignored. Given the rapid growth and widespread usage of air transport, the importance of pressurized air in a cabin is of highest importance. Increased pressure due to high altitudes brings impediments to both the overall structure of the plane and the lives of the passenger. A control process, as described in this article, maintains appropriate pressure in an airplane cabin by utilizing the heat from the exhaust engines to warm the atmospheric air and to compress it to required levels. From the article it can be said that the controlled variable was the cabin pressure, the disturbance is the air flow of the atmospheric air entering the pain and the manipulated variable was the flow if air in the cabin itself. This is a sensible use of variables for this process. The article doesn’t mention any specific sensors used in this process but it would be logical to state that a pressure sensor is used to monitor the pressure of the cabin and the atmosphere (depending on whether the process is feedback, feed forward, or a combination of the two). The disturbance caused by unexpected by pressure drops is a serious one which could be life threatening if a rapid response is not received. Another disturbance variable that could be considered in this process would be that of the breathing of passengers which would initiate a minor air flow in the cabin as well. Given the two controllers PI and PID, it would make the most sense to use the PID controller given its relatively lower over shoot. Considering that we are talking about life critical pressure here, any overshoot which could lead to absurd pressures should be avoided, therefore a PID controller makes most sense here. It was interesting to see the differences in commercial and fighter jets due to the smaller area covered, and how that would lead to a different set of process control. As an regular very long distance flyer, I would certainly keep this article in mind as I tinker over the information on the flight path to kill time.
This blog post discusses the environmental control system on an airplane that provides air supply, thermal control, and cabin pressurization for crew and passengers. A feedback system is in place on an airplane in which cabin pressurization and air flow is monitored and adjusted to the setpoint desired. The air intake from the outside from the compressor stage of the gas turbine engine is adjusted according to the setpoint as well in order to control cabin pressure. This air goes through a process in which it is cooled, humidified, and mixed with recirculated air. This becomes the air that the passengers breathe while they are on the plane. Cabin pressurization is controlled since it is maintained at 11,000 pounds per square inch which is the same as the pressure one would experience at 7,000 feet. The setpoint for this to happen is at the cruise altitude of approximately 35,000ft. When the plane is descends, the reverse occurs when the pilot makes the setpoint the altitude of the destination airport. While the altitude is important is maintaining the cabin pressure, the structural strength of the specific airplane also affects cabin pressurization. For passenger safety, cabin pressurization should be kept below the pressure that one could feel at 25,000 ft. There is an automatic controller that makes sure cabin pressurization is at a safe level for passengers and one that also acts as a safety relief valve. All of these processes are necessary for a safe flight, and such precautions are already taken for cabin safety.
The controlled variables for the environmental control system are the air supply and cabin pressurization. The manipulated variable would be gas turbine engine since it is adjusted to release the amount of air and pressure at the setpoint. Disturbance variables can include unexpected changes in the temperature control of the plane, an emergency landing, or even a bird getting stuck in one of the turbines.
The controller type that would be most appropriate for this product would be the PID controller since it allows for fast response to sudden changes, eliminates oscillations, increases control, and improves stability. Developers of this product can tune the controller of the process by using PID Tuning Software, such as Simulink PID Controller Training, or by using the Ziegler-Nichols tuning method. Using the Ziegler-Nichols tuning method allows for experiments to take place on a closed loop which allows for tuning while the controller is on. By doing this, developers could see how the cabin pressure changes as the controller is adjusted.