We are reporting on a detailed energy assessment of Brick + Mortar and the Simon Silk Mill to perform an economic analysis on what energy-related alternatives can be implemented for cost-savings. Our assessment developed an overview of the technical features of the building and scope out the energy-related aspects. For a future economic analysis to be plausible, we need to be familiar with the windows, walls, HVAC (Heating, Ventilation, Air-Conditioning), and lightbulbs of the studio before providing alternatives. An understanding of these technical aspects allows us to fully collaborate with Mr. Hampton in providing cost-efficient, energy-saving alternatives while striving for the goal of aesthetics.
It’s first important to look at the Simon Silk Mill pre-construction. Prior to any construction, several investigations, detailed below, were done to the site by CMX Engineering to ensure feasibility of the project. These investigations offer information that helped give us a sense of what original developments were necessary for the Silk Mill project and how our proposed changes to Brick + Mortar can reflect those changes for better or for worse if undertaken. Although interesting background information, the investigation reports also helped guide us with practicality in mind so we knew what we are doing is technically possible.
One of the engineering assessments done by CMX Engineering was a structural condition assessment. The assessment and analysis were completed with fairly successful results. The majority of the buildings “are in relatively fair to good condition,” but more importantly they “appear to have adequate structural floor load carrying capacity to enable their adaptive reuse as either residential, office, [or] retail…” facilities. Though, some buildings were in “poor to extremely poor condition,” which led to suggestions of immediate repairs and in some cases, demolition. The cost estimate was set at $3,140,000. The final cost of the repairs is not disclosed in the report as this was done prior to any construction (Lippincott).
The mechanical, electrical, and plumbing (MEP) investigation found that the Simon Silk Mill had a total of 350,000 square feet worth of buildings, consisting of 22 buildings, though only 18 are being used now. The buildings were originally “heated by a central steam heating plant and a network of piping installed in tunnels,” but has now been abandoned and is not in operation. The result of the MEP study claimed that no part of the existing systems could be salvaged and all new systems would have to be bought (Lippincott).
The geotechnical team reported that “any proposed structures can be supported utilizing a shallow foundation system, consisting of strip and/or spread footings and should be designed for a maximum bearing capacity between 2,500 to 3,000 psf.” This gives us insight into what restraints the engineers had when completing their revitalization of the mill. There was also a civil site assessment, which reported information that does not pertain to our study (Lippincott).
Brick + Mortar, specifically, has about 30,085 square feet in space between its gallery and studio (Lippincott). It’s unknown what the exact difference in size is, but the studio is visually larger than the gallery. Both rooms have high ceilings, which means more energy consumption is necessary to heat and cool the rooms. The skylights in the ceilings require additional height in the ceilings because of their tilt, adding additional open space. The gallery, in particular, is mostly open space to create an aesthetically pleasing entrance to where art lines the walls. Artists have to think extensively on how they want to set up their gallery so that their art is best presented. Inside the White Cube is a renowned “ideology” that gallery owners have been referring to since its first book edition in 1986. Its science-like breakdown of art galleries suggest that the best way to present art is by entrapping the gallery from the outside of the world. This is described by a spectator entering one of their recommended gallery types, “in front is an open space in which the viewer’s sense of his own presence becomes an increasingly palpable shadow” and it’s just the art that sticks out. To create this seemingly abstract, unrealistic setting, the gallery owner needs to encompass their space as a ‘white cube’ with white walls and open space, and no outside lighting (O’Doherty). Mr. Hampton is a modern artist, though, and unsurprisingly doesn’t follow a 1986 approach. Although Brick + Mortar takes important aspects like open spaces and white walls, the gallery includes natural lighting from the skylights, rustic ceilings, and stand-out HVAC systems. Since there is a considerable amount of open space, the HVAC units’ efficiency becomes incredibly important.
The HVAC units’ ducting actually differs from each room. It’s possible that the development group suspected two different businesses with two different designs to split up the buildings. It’s attainable for there to be two different designs because although the Silk site uses “a central energy plant that produces and distributes thermal energy for space heating, air conditioning, and industrial purposes from a central site for the buildings,” some or all of the buildings have their own individual HVAC units, like Brick + Mortar (Lippincott). The gallery contains circular shaped ductwork while the studio boasts rectangularly shaped ductwork. Both types have advantages and disadvantages. A round duct tends to be more efficient than a rectangular duct in performing the same task because of it’s smaller cross-sectional area with less duct wall exposed to moving air. For example, an 18-inch diameter round duct has the same air-carrying capacity as a 26-inch wide and 11-inch high rectangular duct. The cross-sectional area of the round duct is 254.5 square inches and has a perimeter of 4.7 feet, while the rectangular duct has 286 square inches of area and a perimeter of 6.2 feet. Due to the 32% increase in metal needed for the rectangular duct, the cost should be proportionately higher. The major disadvantage of having round ducts is the height of it compared to rectangular ducts making it more difficult to fit into spaces. It is unknown why the development group chose these ducts for the room they chose them for, but it can be inferred that they needed to shape the ducts in a specific way for each room (HVAC Equipment).
Heating and cooling are most contributed by the building’s HVAC system, but also by its lighting, windows, casements and ceiling and wall materials. The gallery has four framed door windows at the entrance with a large stationary window above (Photo A) and a smaller single hung window to the side (Photo B). The two bigger windows are thin and have cheap plastic casing while the door windows are slightly thicker and installed within the thickness of the doors. Various materials for window casing offers different amounts of insulation. Plastic offers poor insulation due to their lack of density while metals conduct heat too easily. Wood would be a more reasonable option. Another option is to apply an insulated window glazing. Purchasing windows with low-emissivity coatings applied to them is an option to reduce energy loss by as much as 30% to 50%, though they cost about 10% to 15% more than regular windows (Window Types).
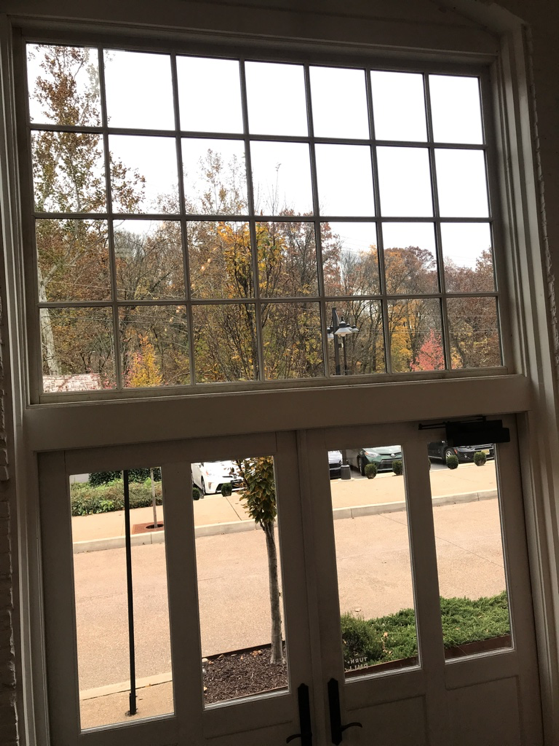
Photo A. Entrance doors to the gallery with a large window on top. Self-taken.
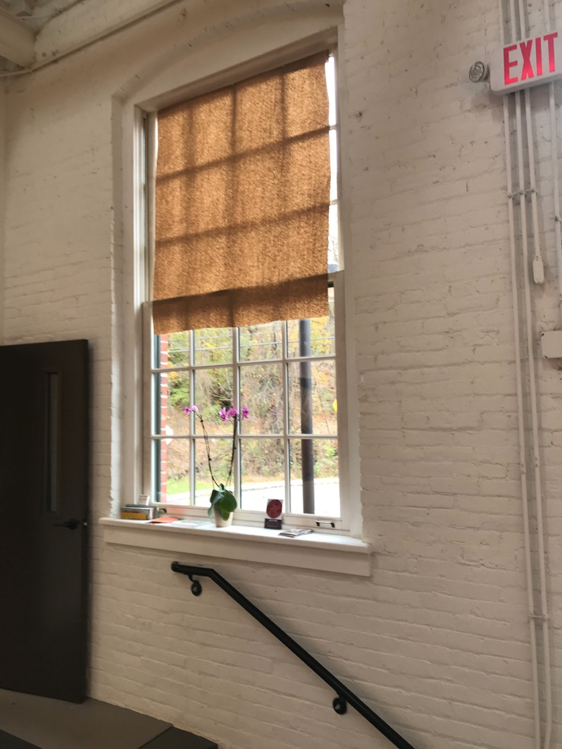
Photo B. Single hung window in the gallery. Self-taken.
The gallery also contains four skylight windows (Photo C). Although the skylight windows naturally light up the gallery positively, mounted lights are necessary for cloudy days, nighttime, and showings. In addition, the skylight windows are poorly secured in the ceiling with visual gaps between the edges and the ceiling. The gallery has forty-five 75w Philips incandescent light bulbs held by the same number of Juno T219 fixtures (Photo C). Incandescent lighting is known to be the least energy-efficient form of lighting on the market (Department of Energy). Better options are compact fluorescent lamps (CFLs) and light emitting diodes (LEDs) (Department of Energy). The U.S. Department of Energy reported a comparison of newer lighting versus the traditional incandescent lighting, which is no longer manufactured, based on a usage of 2 hours per day with an electricity rate of 11 cents per kilowatt-hour. Brick + Mortar’s type of lighting only saves about 25% of energy costs versus the traditional incandescent lighting compared to ~75%-80% in savings from CFL and LED lighting.
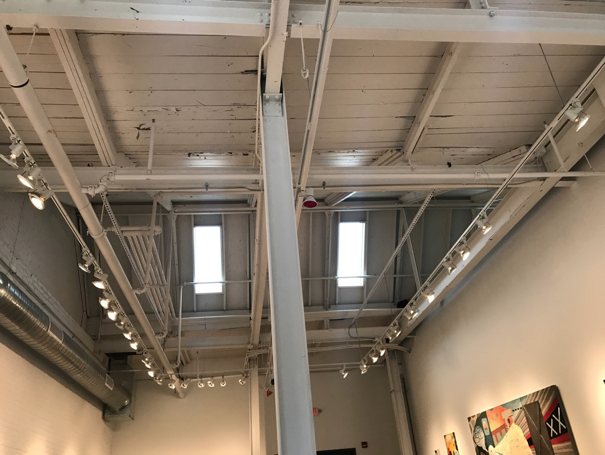
Photo C. Two of the four skylight windows in the gallery and part of the lighting tracks. Self-taken.
In the studio, there is lighting similar to the gallery, but in shapes of tubes. The studio has six skylight windows compared to the four in the gallery, which makes sense because it’s larger in size. The studio also has a large window on the street-side wall and a small square window on the parking lot-side wall. The most distinct features of the studio are the two garage doors (Photo D). They allow for a loading dock and are nearly the height of the beginning of the ceiling. Although the garage doors had to remain when Mr. Hampton moved in, he had options on their materials. For aesthetic reasons, he chose the option that is least energy-efficient. By observation, these garage doors lack insulation immensely and airflow can easily be felt when standing nearby. The building is also south-facing meaning the garage doors get direct sunlight. Direct sunlight through cheap windows can translate heat into the building very easily requiring more air conditioning.
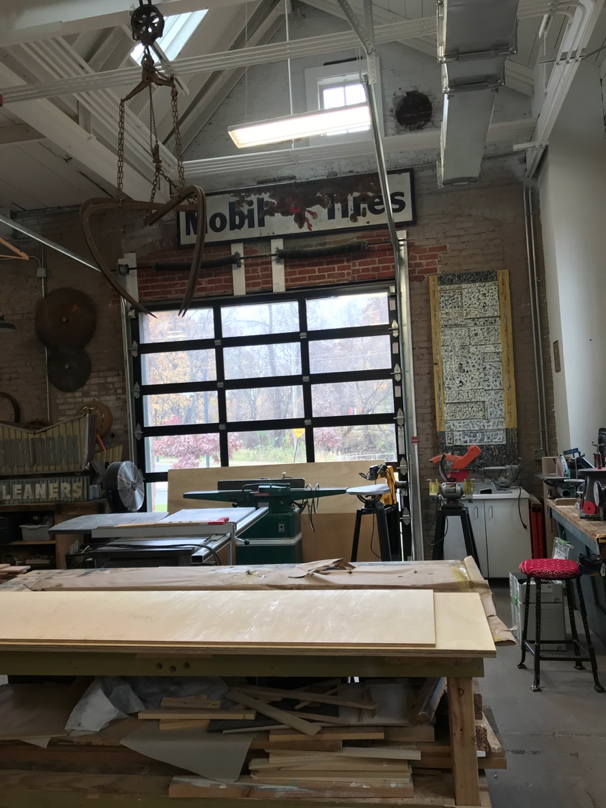
Photo D. One of the two studio garage doors.
To a lesser extent, airflow can be felt while standing near any other window or door. A limitation to our assessment is measuring the airflow and being able to come to a conclusion on why they are leaking as much outside air as they are. We do not have the materials or time to research the extent of these implications, though we can speculate that the poor-insulating materials and gaps between the wall and casements create unnecessary energy costs. A possible, perhaps temporary, solution to filling the gaps is by using a spray polyurethane foam. Sold by various retailers, one claims that the spray “expands and cures quickly to fill gaps, expansion joints, and more” (The Home Depot). A simple fix such as filling the gaps between the wall and casements is a cost-effective technical solution that requires minimal maintenance and is able to better insulate the studio.
The wall and floor materials are also important features to consider. The floor throughout the building is made up of concrete. Concrete can achieve thermal stability by insulating the “almost constant” earth temperature that it lies on. Although, Mr. Hampton had told us there was a basement under their space, which leaves us to question whether it’s the right material. They have other elements, though, like absorbing radiant heat from indoor heating units. When heating is required in the winter, “the thermal mass will help keep a dwelling warm and reduce heating energy consumption” (Concrete Slab-on-ground). Due to its controlling nature, the concrete can absorb the heat during the day and release at night when the temperature decreases. Additional glazing can help emphasize concrete’s ability to stabilize thermal comfort.
Different from the floors, many of the walls are made of brick. The obvious reason for the development group to build or reconstruct the Silk buildings out of brick is for the rustic appearance to represent its history. Brick may fit the aesthetic nature of the site, but it’s not a very good insulating material. It’s thermal resistance, or R-value (m2 ℃/W), is 0.27 per inch (Briga-Sa) compared to a range of 0.71 to 1.41 per inch for various types of wood (Department of Energy). A higher thermal resistance notes more effective insulating properties.
If implemented, there are several alternatives that can reduce energy costs. Though, for someone to decide between several alternatives, it’s necessary to be presented with a quantifiable difference. Performing economic analyses will define the alternatives in a way for Mr. Hampton to decide if the values can justify alterations to his building’s aesthetics.