Crystalline Silicon
There are two general types crystalline silicon photovoltaics, monocrystalline and multicrystalline, both of which are wafer-based. Monocrystalline semiconductor wafers are cut from single-crystal silicon ingots as opposed to multicrystsalline semiconductor wafers which are grown in thin sheets or are cut from directionally solidified blocks. Monocrystalline ignots are more energy intensive, expensive, and generally more difficult to grow than simple blocks of multicrystalline silicon [4]. Monocrystalline silicon is the most efficient photovoltaic (PV) cell with a market efficiency of about 14-18% [3]. Compared to monocrystalline silicon, multicrystalline silicon PV cell is moderately efficient with a market efficiency ranging from 11-14%, as a result, the cost of multicrystalline is slightly less than the cost of monocrystalline [3].
Currently, crystalline silicon technology is the most efficient form of solar photovoltaics. Crystalline silicon technologies make up about 85% of the photovoltaic market [1,4], this is largely because crystalline silicon technology has established operational lifetimes of 25 years [4]. Due to its high efficiency, crystalline silicon panels require less space in order to generate the same amount of energy compared to other existing photovoltaic technology. Moreover, silicon cells are currently dominating the residential terrestrial solar sector [2].
Monocrystalline Silicon
- Highest market efficiency
- Cells: 15-20% [3]
- Modules: 20-25% [2]
- Highest Cost: $2 to $5 per watt for PV cell [3]
- Most commonly used
- Cut from single-crystal silicon ingots
- Thick wafers: 200-400 μm [3]
Polycrystalline (or Multicrystalline) Silicon
- High market efficiency
- Cells: 13-16% [3]
- Modules: 15-20% [2]
- High Cost
- Faster production than monocrystalline silicon [4]
- Molten silicon cast into ingots
- Thick wafers: 200-400 μm [3]
Thin-Film
Thin-film technology is the least expensive photovoltaic alternative, and yet, it is not as widely used as crystalline cells and modules. This is largely due to the fact that thin-films are the least efficient photovoltaic option and subsequently, thin-film technology have a much lower lifespan than crystalline technology. Additionally, due to the low efficiencies of thin-film technology, a much greater amount of space is required compared to crystalline panels in order to generate the same amount of energy. For example, the installation area required for cadmium telluride (CdTe) module is double the area required to install multicrystalline silicon modules [2]. Not only is more land required for thin-film due to its low efficiencies, thin-film may also require more materials, labor, and consequently installation and maintenance costs in addition to the the initial cost of the cells/modules. The most commonly used thin-film cells are made of amorphous silicon but there are other types of thin-film photovoltaics entering the market, including copper indium diselenide, cadmium telluride, and gallium arsenide [3]. The non-crystalline nature of thin-film cells has had intrinsic limitations on its efficiency, resulting in a much lower market share compared to large crystalline silicon [2], but as the market for thin-film technology has grown due to its low cost and “thin” nature, the applications for thin-film have become more versatile.
Amorphous Silicon (a-Si)
Amorphous silicon is the least efficient and least expensive option, with an efficiency that is slightly less than half that of mono- and multi-crystalline silicon [2]. However, compared to large crystalline silicon technology, amorphous silicon uses only about 1% of the material [3].
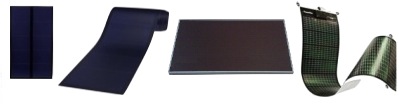
Different forms of thin-film Amorphous Silicon panels
- Low market efficiency
- Cell: 8-10% [3]
- Module: 6-9% [4]
- Low Cost
- a-Si cell costs $2 to $3 per watt [3]
- Thin-film: 2 μm [3]
Other Types of Thin-Film
Copper Indium Gallium Selenide and Copper Indium Diselenide (CIGS/CIS), Cadmium Telluride (CdTe) & Gallium Arsenide (GaAS)
- Expected lifespan less than crystalline panels
- Least efficient
- cell: 14-20% [3]
- Inexpensive
- Thin-film cells cost about $1 to $4 per watt [3]
- Layers of different PV materials are applied sequentially to a substrate directly deposited on a glass, plastic, stainless steel, ceramic, or other compatible substrate material [4]
Copper Indium Gallium Selenide & Copper Indium Diselenide (CIGS/CIS)
- market efficiency for cell: 8-12% [3]
- market efficiency for module: 8-14% [4]
Cadmium Telluride (CdTe)
- market efficiency for cell: 10-13% [3]
- market efficiency for module: 9-12% [4]
NOTE: String-ribbon silicon is another way of saying multicrystalline silicon strips
Author: Abby Studen
Editors: Hannah Goldstein, Kevin Jackson
Sources:
[1] Data from: EPIA (2014). Solar cell manufacturing: global production by type 1999-2011. p. 43. accessed through Statistica. Web.
[2] Fraas, Lewis. Low-cost Solar Electric Power. Springer, 2014: 1-42. Print.
[3] Patel, M. (2006). Wind and Solar Power Systems: Design, Analysis, and Operation (2nd ed.). Boca Raton, FL: Taylor & Francis. Print.
[4] U.S. Department of Energy. Sunshot Vision Study. Feb 2012.