1. Industrial Strength Prosthetic Arm
-Prosthetic arms are built for everyday tasks, with an emphasis on convenience, and precision. We could design a more sturdy version that
would use different materials and allow for more strength and durability, at the expense of weight and precision.
-We believe that the current prosthetics are weak.
-Uses: picking up heavy materials
2. Large Robot Hand Mimic
-A large mechanical hand, with steel for bones, and hinges for joints, ect, servos could replicate muscle and wires, like those in a bicycle’s brakes could act as tendons. We could wire the hand to a glove with sensors, so it would mimic the movements of the person wearing the glove. The glove would likely be a rigid shape, with hinges for each of the joints in the hand that would be mimicked by the robot hand.
3. Bionic cast
– A large metal or composite structure with force sensors built in throughout the length of the
cast. Force sensors allow the cast to be removed and automatically reset based on the user’s needs. Allows for better cleaning, and all around access to the broken area compared to traditional casts. Is most likely made up of bands and latches that can contour to different parts of the body and different shaped users.
4. Better designed crutches
– Crutches may be uncomfortable and cause shoulder rib and hand pain the way they are currently designed. It could be interesting to look into redesigning them so they put less strain on the user, which we could do by incorporating a robotic element that would be able to help with keeping the weight off of the users shoulders. There could also be sensors that could be able to autocorrect the crutch if the user is off balance. We could also look into the materials side and see if we can make them lighter and foldable so that they would be easier to put away when they’re not being used (like if you were traveling in a car for example).
5. Robotic elbow/arm brace
– Much like the mechanical knee braces that injured athletes wear. We could base our design off of how the knee braces work and try to alter that to suit our arms. The main idea of this brace would be to try and support people with nervous system disorders affecting their arms, namely Parkinson’s Disease. The material would have to be relatively durable but not heavy. Less robotics may be incorporated into the design but that all depends on how complicated we decide to make it. The brace could include position sensors and adjust according to the collected data or it could just be a mechanical brace designed to just lessen jerky or rushed movement.
6. Robotic knee or ankle brace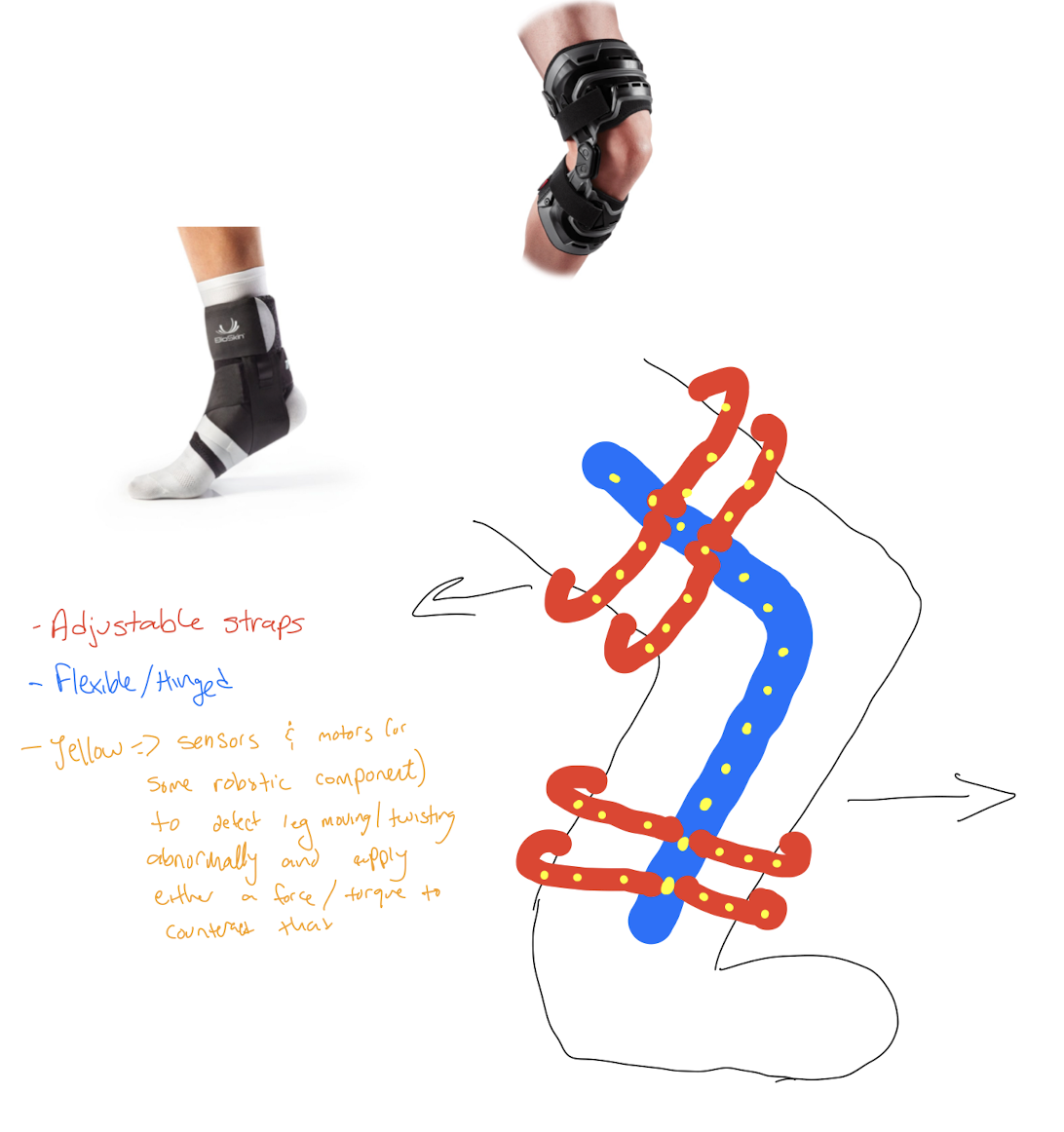
-Some ligament injuries (i.e. ACL tears, ankle sprains) occur when the ligaments twist. ACL tears sometimes happen because of quick changes in direction, where upper leg essentially moves in opposite direction of lower leg; ankle sprains commonly occur when you “roll an ankle,” stretching or twisting ligaments
-Using the idea of fall prevention exoskeletons, that uses sensors to recognize when a person has lost their balance and applies a force to the hips to counterbalance the slip, thus preventing a fall. This idea could be applied to knee or ankle braces, to apply a force counteracting the direction the joint is moving, essentially forcing it back in its correct position, ideally before any serious injury occurs.
7. Football Helmet
Football helmet built with sensor and a rotational motion stabilizer that would help limit concussions by reducing the force of the hit.
8. All Terrain Type Drone
– It’d seem like straight out of a movie, but a drone that would be able to drive, fly, and swim seems like a very interesting project. Design-wise, it is still just up in the air (no pun intended!), but it could be more flat with various propellers and a motor in the back. The issue is that boat motors are usually large and heavy which is part of the reason it will never be able to fly. Weight can be saved by using the same motorist drive all the wheels and propellers with different gear shifts. Rotating axels connecting each propeller would allow it to seemingly travel from one medium to another.